Highly engaged employees aligned with the safety program make the company money, reduce turnover and lower incident rates.
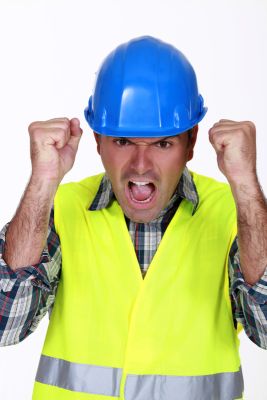
Safety is fast becoming the best tool to recruit, hire and retain good people. Simply put, when yours is the best and safest place to work, you will attract and retain the best employees. But if your employees identify with even a few points on the list below, you will have some work to do in finding good people and, more importantly, hanging on to the good ones you have.
Companies may want employees to buy-in to safety, especially at safety meetings, but safety has to do a better job of being consistent with its message and how safety is represented - especially in front of employees.
Having attended hundreds of safety meetings, I have compiled a starter list of 21 reasons why employees are confused, confounded or frustrated by safety - reasons that prevent employee buy-in to the safety program. This is not a complete list but it is a good start:
- Senior managers who preach safety's importance but rarely attend safety meetings - and if they do attend, they claim they can't stick around for the rest of the safety day due to “more pressing” things to look after
- Boring, unfocused safety speeches by boring, unfocused safety personnel that use text-laden corporate karaoke PowerPoint rehashes of the same things they discuss every month
- Safety managers who don’t bother to improve their presentation and engagement skills yet who chastise employees for not improving their safety performance
- Senior managers who don't take the time to come out of their offices and spend some time with front-line workers, asking questions and engaging in discussions about safety
- Feeling like every safety meeting is a scolding session and a one-way lecture - like they used to get from the school principal
- Safety “discussions” that do not allow for employees to voice their concerns or opinions on safety and are instead, lectured to and told what to do
- Explaining the what, when, where and how of safety procedures but the "why" of the procedures is not explained making the safety program look like a narrow set of rules
- Feeling under-valued or under-recognized for what employees do right but being scolded for when they do it wrong
- The worst safety yahoos on-site are recognized for years of safe service when, in fact, it has been years of "lucky" service
- Being forced to play childish games like safety bingo and being rewarded with crappy trinkets that devalue a safety program
- Safety officers who suck the fun out of going to work by making rules enforcement more important than coaching employees to better safety performance
- Suffering through mountains of paperwork and petty bureaucracy without explaining why the paperwork is necessary and how it helps reduce incident numbers
- Punishing an entire crew with procedural refreshers and long bouts of retraining instead of dealing directly with the one or two employees who fail to follow procedures
- Carbon-copy safety training that is exactly the same for each employee without consideration for individual learning ability or past safety training
- Being forced to work alongside invincible employees who think that incidents won't happen to them because safety training is only for idiots
- When employees are pushed hard for production but have been told that safety is most important - which compromises the very safety program they are told to follow
- Safety personnel with a sense of entitlement who wield their power over others by way of their certification in safety
- Resenting being told by the safety guy how to do the job - a job the safety guy has never done
- Safety people who think they are smarter than everyone else and who not taken the time to earn the respect of employees before spouting off
- Being trained in the job and then being handed over to the safety department to be trained there - as though the two departments can operate independently
- Being forced to pee in a cup while managers are allowed to attend management retreats with an open bar - managers who set corporate policy on safety issues
Frustrated employees turn over. Employee turnover means higher costs for recruiting, training and lower production output. Highly engaged employees aligned with the safety program make the company money, reduce turnover and lower incident rates.
Safety buy-in is important for recruitment and for future business. Businesses with substandard safety records will start to feel the pinch soon. Companies don’t want to be associated with companies with poor safety records. Your safety record will be a key consideration in how well your company performs financially. When your company becomes an exceptional safety performer, you will find that more companies want to do business with you.
To become an exceptional safety performer, you need to have your employees on-board with the safety program. That requires buy-in - not just compliance. When employees buy-in, they believe in safety and will support and align with the safety program. They will do the right thing when no one is looking.
For a little extra help in getting the communications part of safety right, download my free e-book, 7 Nuts 'n Bolts Strategies For Safety Communication below.