6 minimum standards that are preventing you from establishing a strong safety culture.
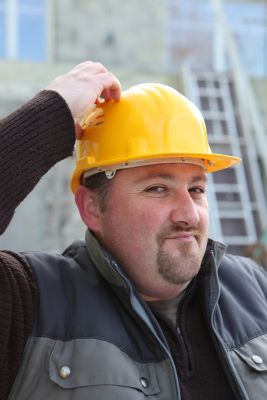
No one wants to see anyone injured. To build a safety culture requires more than just viewing safety as an injury-prevention program. It’s more than following rules and meeting minimum standards. To build a safety culture requires employees to be respectful of each other, to display courtesy and care about each other. Safety is a teamwork philosophy.
There are six overlooked areas considered minimum standards that are preventing you from establishing a strong safety culture. Here is the list - and how to fix them:
1Competence. It’s a minimum standard allowed by an employer. Anything less than competence is incompetence. The line between the two is narrow.
Fix: Don’t aim for competence. Go beyond. Aim for mastery in job function and in safety. Set a higher standard to become exceptional in your work. The desire to want to protect your exceptional ability will follow. The best people doing the best work in the best safety program are more than just competent.
2COR (Certificate of Recognition). It’s a minimum market-driven standard today. Any company without a COR will find it difficult to attract new business. Those without COR certification find themselves squeezed in the market. According to Alberta Jobs, Skills Training and Labour, “it is not unusual for Alberta corporations to expect contractors bidding on contracts to hold a valid COR.” That makes COR a minimum market-driven standard.
Fix: If you don’t have your COR, you’re already behind. Getting a “COR” is easy when the company’s “CORe” values include safety. Safety can no longer be an add-on to existing work. It must become the basis and foundation of how you work. Make it a corporate mission to achieve every safety certification possible.
3Compliance. It is a minimum standard of conduct expected in the Occupational Health & Safety Code. Non-compliance is enforceable by penalty or consequence. Compliance is the minimum standard offered up by the OHS Act, Regulation and Code. The law requires you to meet these minimum standards.
Fix: When you focus only on meeting minimum standards, you are one bad test away from a failing grade - just like “D” students in school. Hold yourself to a much higher standard. Like competence above, consider achieving mastery in safety. Ask your employees to buy-in to safety as a personal value.
4Safety meetings. Stand-downs and toolbox/tailgate meetings are a basic minimum standard for each workplace. As a legal requirement, safety meetings have become information dumps, one-way broadcasts and lectures. Workers sit through these events with no paper, no pens and no way to recollect anything presented. Employee participation is not required, only attendance.
Fix: Replace the lecture-style safety meeting. That includes you, PowerPoint prophets. Consider a format more reminiscent of a Town Hall discussion on safety in which everyone participates. Include new ideas. Invite plenty of outside perspectives. Offer employees inspiration to embrace safety as a personal value as part of your safety meetings.
5ARIH (Advertise-Resume-Interview-Hire). The old model of chasing after workers is a minimum standard. When you have high turnover or inconsistent work, you make employees disposable. People will choose to go to where the work, the workplace and corporate values are safest. Workers with strong personal values around safety are not attracted to minimum-standard safety programs. If your workplace doesn’t subscribe to a higher standard, you will have to choose from the pool of workers bouncing from job to job. “Now Hiring” ads and signs demonstrate your inability to attract a long line of good candidates.
Fix: The best place to work is the safest place to work. Period. A strong safety culture is your best employee recruitment, attraction and retention tool. A strong safety culture attracts and keeps good employees with strong values around safety. People want to work where they feel respected and valued. Nothing shows that better than a safety culture that protects and cherishes its employees.
6Hierarchical management. This management model is a minimum standard and practically useless in safety. You cannot legislate employees to buy-in to safety. At best, in a hierarchy, employees will tolerate rules. Top-down directives to obey the safety rules don’t inspire a worker’s best performance. It only inspires enough to not get fired.
Fix: Safety Leadership is the new management model. Encourage every worker to show their leadership ability. Spread safety responsibility around. Make all workers equal. The main principle of safety leadership is that employees do not work for management. Management works for employees providing skill development, coaching, inspiration and mentoring.
To move from minimum standards to a strong safety culture requires more than new procedures. It requires a philosophical shift in corporate values: one where employees are valued over everything else. Good employees with good values doing good work make good money - for themselves and the company. Start with protecting your employees. They will protect you.